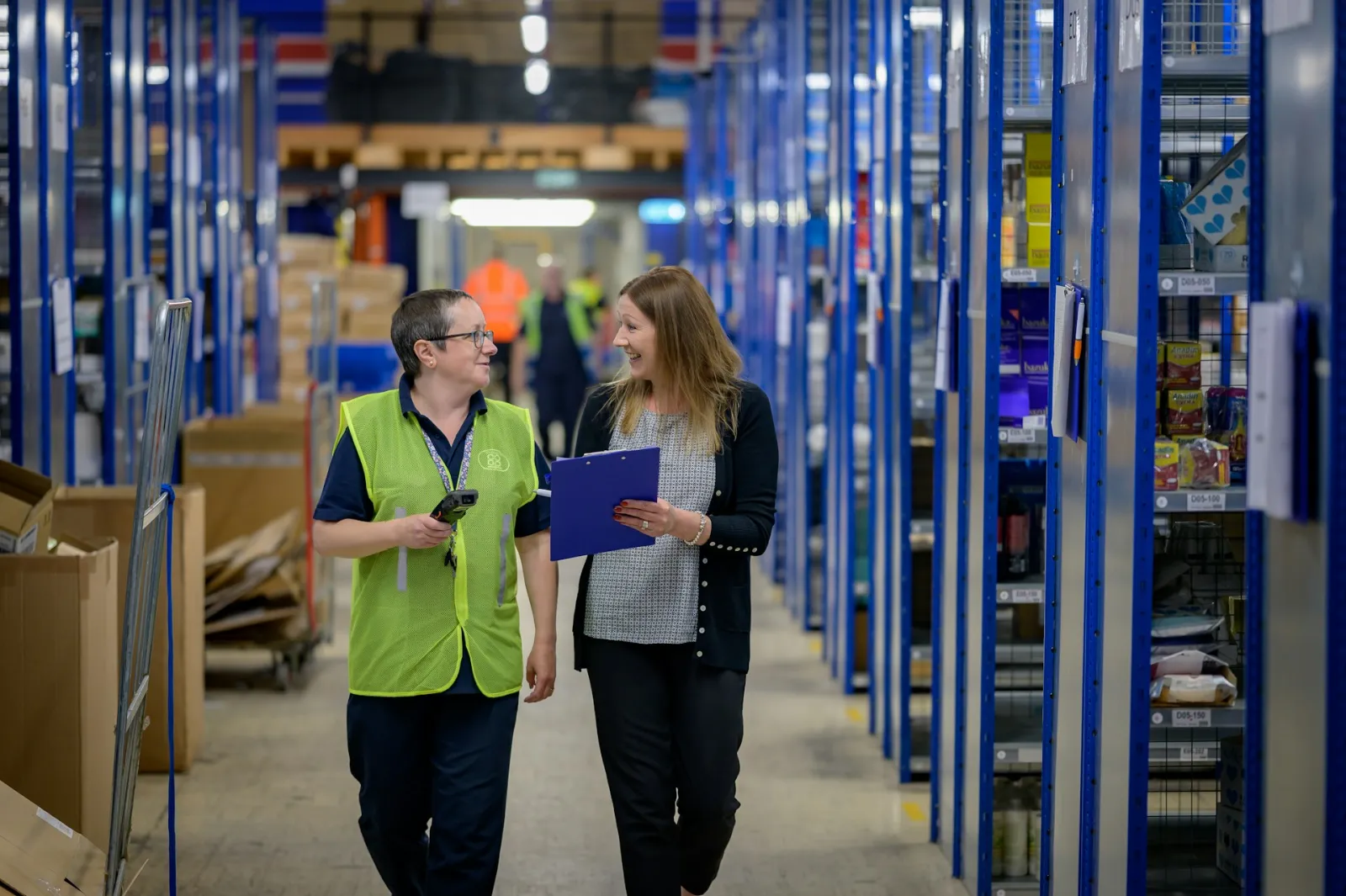
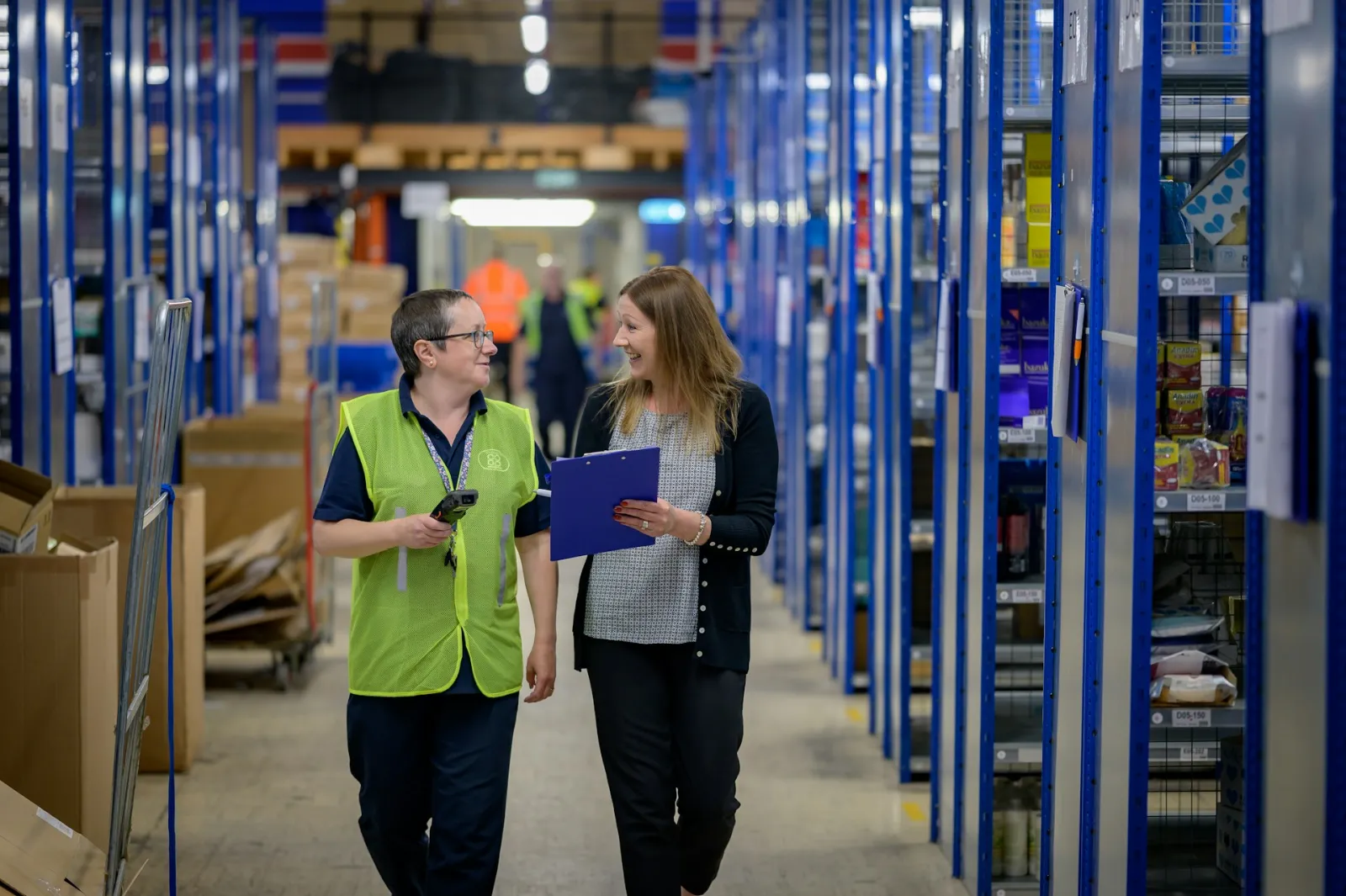
Where in the Workplace Should You Put Your Spill Kit?
With anything safety-related, there are all kinds of dos and don’ts to be aware of. Some are obvious, some less so, and spill kits are no exception. Simply having them in your workplace isn’t enough: you need to know how to use them effectively too. Storage is a significant part of this. Spill kits should be appropriately located and safely stored, not only to prevent them from being damaged or mislaid but to ensure that they’re within easy reach if a spill does occur.
If you’re unsure where to store spill kits in an office, a warehouse, a manufacturing facility or any other workplace, we’re here to help. In this comprehensive guide, we’re going to run through recommended spill kit placement guidelines for a wide variety of different workplaces, explaining how to determine the best placement and covering the various spill kit storage solutions available.
Which workplaces need spill kits?
First off, let’s start with the basics: does your workplace need a spill kit at all? According to the Environment Agency’s Pollution Prevention Guideline 26 (PPG 26), spill kits containing leak-sealing putty, over-drums, drain seals, oil or chemical absorbents and personal protective equipment (PPE) should be on-site at any workplace where the risk of spillage is present.
From oil and fuel to chemicals and solvents, spill kits can be used to tackle a wide variety of different spillages – but not every workplace needs one. In office environments, for instance, there is typically no risk of a significant spill occurring, meaning a spill kit is usually not required.
However, in any environment where significant volumes of liquid are being stored, decanted or transferred from container to container, a spill kit (or multiple) should be on-site at all times. Such environments can include everything from commercial kitchens to vehicle refuelling areas, warehouses, factories, retail stores and workshops. If spills are recognised as a potential risk in your workplace, spill kits are an absolute must.
Ideal places for workplace spill kits
So, what are the optimal locations for spill kits? There are countless different regulations surrounding workplace spillages, including specific requirements for IBCs, drums and pallets. However, in the UK, there is no specific legislation relating to spill kits; other than the fact that they must be located on-site and that staff must be trained on how to use them, the location and storage of spill kits are open to interpretation.
This lack of clear-cut guidelines sometimes leads to confusion, with many businesses struggling to determine the best possible location for their spill kit station. However, the answer to this dilemma is actually pretty simple.
In short, spill kits should be located as close as possible to high-risk areas. Following any chemical spill, a rapid response is essential in order to prevent environmental damage. With that in mind, your spill kits should be within easy reach at all times, allowing your employees to respond quickly and contain the spill.
Any high-risk area (such as a location where chemicals are stored, transferred or decanted) should have a spill kit present, ideally within a 20-30 metre radius. Obviously, the closer the kit is to any potential spill the better, but there’s no need to have multiple nearby: just make sure there’s an appropriately sized kit within easy reach.
How to improve spill kit accessibility in the workplace
It’s not just the location of each spill kit that matters, but how visible they are. To ensure that spill kits are easily accessible and that the right kit is used for the right type of spillage, there are two crucial aspects to consider: labelling and training.
Although all spill kits come with suitable labelling and brief usage instructions as standard, it’s important to ensure that these labels and instructions are in good condition and clear. In a high-pressure situation, your team will need to read the text present on the spill kit quickly; if it has degraded or worn away over time, new labels and instructions should be applied.
Besides the labels on the kit itself, the location of the kit should also be clearly marked. Once you’ve selected a suitable area, make sure it’s clearly signposted; the location should be clear from every direction, allowing employees to spot the kit and respond to any spillages quickly and efficiently. Any confusion during the early stages of a spillage can mean precious seconds are lost, potentially leading to unnecessary property and environmental damage.
As well as signposting the location, you should clearly state which type of spill kit is stored there. Employees should be able to work out which type of kit is present before they retrieve it and look at the label on the kit, again costing precious seconds. When you install signage, you might want to add the spill kit type to the sign too. For example, oil and fuel, chemical or general purpose.
In addition to installing signage, make sure that the location of the spill kit is well-lit. If you choose a location in the corner of your warehouse or store room, for instance, make sure there’s adequate lighting in place. Should a spill occur after the sun sets, the kit still needs to be easy to find.
Finally, there’s training. All relevant team members should be trained on the usage of spill kits and should be aware of their locations within the workplace. If anything does change, employees should be kept up to date; period refresher courses are a smart idea, just to be certain that your team knows exactly what to do should a spill occur.
Choosing a suitable spill kit
So, now you know where to locate your spill kits and how to make sure they’re used correctly, the next step is to choose the correct spill kits for your workplace. Three main types of kit are available: general purpose, oil and fuel and chemical. Each type contains a slightly different selection of items, and each type is suitable for different spills. There are even more specialised kits designed to tackle the likes of AdBlue and body fluid spills. With that in mind, choosing the right kit is all-important.
There’s size to consider, too. Although there are no clear regulations governing the size of spill kit you should choose for your workplace, there are best practices that should be adhered to.
If you’re interested in learning more about the different types of spill kits available and how to choose the right one for your workplace, check out our guide to choosing spill kits and refills.
Don’t overlook maintenance
Last but by no means least, maintenance. All kits should be regularly checked to ensure they are in good condition and that they include all of the necessary items required to contain and clear up a spill. If a kit is used, don’t forget to purchase any necessary refills in readiness for a future spill.
Whether you need refills for your existing kits or are starting afresh and are looking to buy your very first spill kit, Spillshop is the place to be. With a vast range of options to choose from and an experienced team on hand to offer advice, there’s no better way to safeguard your workplace against the risk of spillage. Discover our complete range of spill kits today.